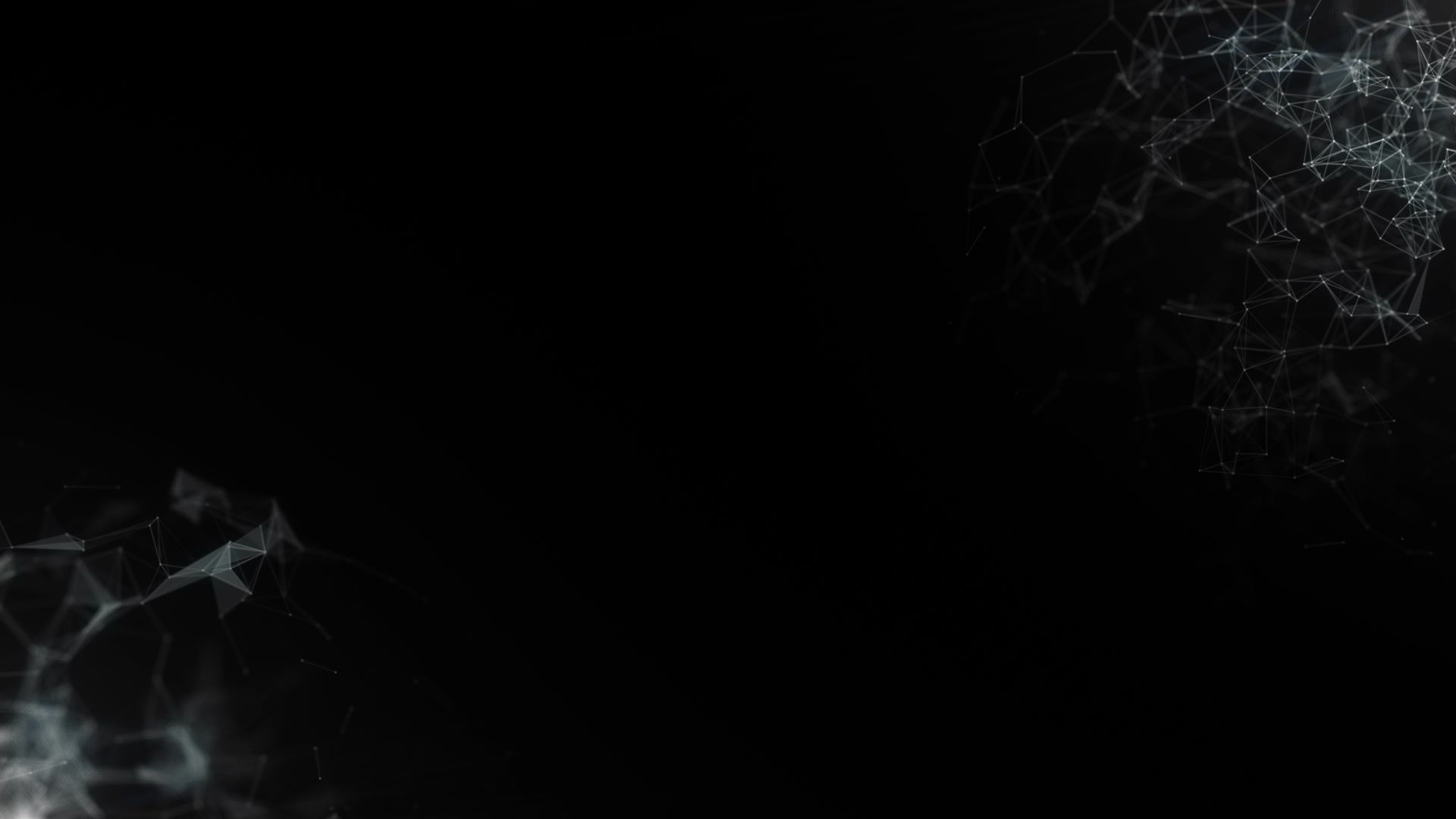
SDCAE RESEARCH LAB.
Advanced CAE Simulation and Experimental Test Solutions
SDCAE lab. has been providing advanced CAE analyses and engineering verification solutions.
Our director's long-time special R&D experiences
- In-house code development experiences for computational aeroelasticity, FSI, and FIV.
- CAE analysis and evaluation experiences for various mechanical systems
- Renewable energy system reseach.
- Development of experimental tests and real-time measurements system
Major R&D Fields:
- Advanced stuructural dynamics and multi-body dynamics (MBD)*
- Multi-physics (multidisciplinary) coupling analysis (CFD+FEM+CSD+MBD)*
- Computational aeroelastic analyses for airplane and helicopter (using FSIPRO2D and FSIPRO3D)**
- Virtual flight load and flutter test simulation methodolgy considering aeroelastic vibration
- Computational aero-acoustic analysis considering aeroelastic vibration effect
- Hydrodynamics and multi-body dynamics coupling analysis (floating offshore platform)
- Fluid-structure interaction (FSI) analysis and flow-induced vibration (FIV) analysis
- Dynamic finite element model updating methodology based on the vibration test
- Developments of in-house codes for coupled CAE analysis
- Steel and concrete floating offshore plaform design and development*
- Floating offshore wind turbine (FOWT) design and development*
- Airborne wind turbine (AWT) design and development including FSI analysis methodology
- Advanced load analyses of wind (on shore and offshore), airborne, and current turbines*
- Load and stability analyses of ground effect vehicle (GEV) and wind-in-ground-effect (WIG)
- Ultra light hybrid sructure design, analysis, and manufacturing using 3D Printer and CC materials
- Real-time test and measurement based on a telemety system (using NI Labview)
- Operating large wind tunnel testing center (size: 8mx8mx30m, max Speed = 45 m/s)*
- Structural mock-up manufacturing service using a large 3D printer (Fortus 900mc)
OUR R&D AND ENGINEERING
SERVICES
R&D Fields
Total Engineering Solutions Using Advanced CAE
Fluid-Structure Interaction (FSI), Flow-Induced Vibration (FIV), and Wave-Induced Vibration (WIV)
In-house Code Development for Numerical Analysis
Wind and Current Turbines
Renewable Energy System
Airborne and Floating Offshore Platform Design, Analysis, and Test
Experimental Test and Real-time measurement including telemetry system design
Efficient proto-type design and manufacturing using 3D printer
Developmen of new concept experimental test machine
On-Going R&D Topic for Joint Venture Product
Ultra Light Structure Design
Micro-telemetry systems
Mechatronics new products
High-efficient Renewable Energy System (Wind Turbine, Current Turbine, Wind-solar hybrid power system etc.)
Advanced CAE Simulations
CFD: Steady and Unsteady Flow Analysis (Multi-phase flow, Aeroacoustic)
PANEL Method: Hydrodynamic Analysis, subsonic Doublet Lattice Method (DLM), supersonic Doublet Point Method (DPM), Transonic Small Disturbance (TSD), Full Potential (FP) Theories
FEM: Linear and Nonlinear Structural Analysis (Stress, Thermal, Buckling, Hyperelastic, Viscoelastic etc.)
FEM: Linear and Nonlinear Vibration Analysis (Modal, Frequency Response, Transient Response, Random, Freeplay, Friction, Hyperelastic etc.)
FEM: Nonlinear Multi-body Dynamics (Rigid and Flextible)
FEM: Fatigue Analysis
FEM: Nonliear Explicit Analysis
(Bird strike, impact and crash etc.)
CFD+FEM+MBD Coupling Method:
*2-Way Coupling Analysis
*Fluid-Structure Interaction (FSI) Analysis
*Flow-Induced Vibration (FIV)Analysis (Heat-exchanger etc.)
*Transonic, supersonic, and hypersonic nonlinear aeroelastic analysis
Potential+MBD+FEM Coupling:
*Wave-Structure Interaction (WSI) Analysis
*Wave-Induced Vibration (WIV) Analysis
FMBD+Controller Coupling:
Flexible Multi-body Dynamics (FMBD) + Controller Model Nonlinear Coupling Analysis
Combined Load Analysis:
Fluid+Structure+Intertia loads
Fatigue loads analysis
Wind turbine extreme load analysis (GH Bladed and FAST code)
Optimum Blade Design:
Horizontal-axis wind turbine
Ducted wind turbine
Vertical-axis wind turbine
New concept WT blade
Airborne WT blade
Current turbine blade with the minimized cavity characteristic
Water power turbine blade
Steam turbine blade (6 stage)
Experimental Test Facility
Real-time experimental test measurements
- NI Labview (cRIO, DAQ etc.)
- Labview SW
Dynamometer Test System
- 4 sets
Large Wind Tunnel**
- Tunnel size: 8 m x 8 m x 30 m
- Max wind speed: 45 m/s
- HAWT and VAWT Wind Turbines
- Industrial system (e.g. Rador under typhoon condition)
Fundamental structural and vibration test equipments
Strain guage, LDS, RPM, temperature, atmospheric pressure, Impact hammer, and accelerometer sensors etc.
Wide Range 3D Laser Scanner
- FARO Focus X30
- Error bound: 2 mm
- Max scanning range: 100 m
Large 3D printer:
- FORTUS 900 mc
- Manufacting size:
0.9 m x 0.6 m x 0.6 m
- Material: ABS and ULTEM
Laser Cutting Machine
Computational Facility
High performance servers:
2 units
AMD Server: 64 core
Ryzen Threadripper PRO 3995WX
384 GB Ram
10 units
DELL 7800 series, 16~24 cores, 256GB RAM, 1 SSD 512 GB, 6~8TB HDD
Data server: 100 TB x 2 EA
System Design, Analysis, and Production
Wind Turbine (WT)
High Performance HAWT
High Performance VAWT
Floating Offshore WT
Airborne WT
Current Turbine
Water Power Turbine
Steam Turbine
Airborne System
Steel and Concrete Offshore Floating Structure (Barge, Floating Dock, etc.)
Light UAV
Small WIG Ship
Gyro-copter UAV
Experimental test machine (5 MW WT coupling test machine etc.)
Large industrial wind tunnel (engine powerd)
(8m x 8m wind area or higher)
Offshore electic cable winding machine
Composite Rador Dom Structure
Extreme pressure composite tank with titanium liner
Electric generator dynamo-testing machine with real-time measurement equipments and GUI control SW
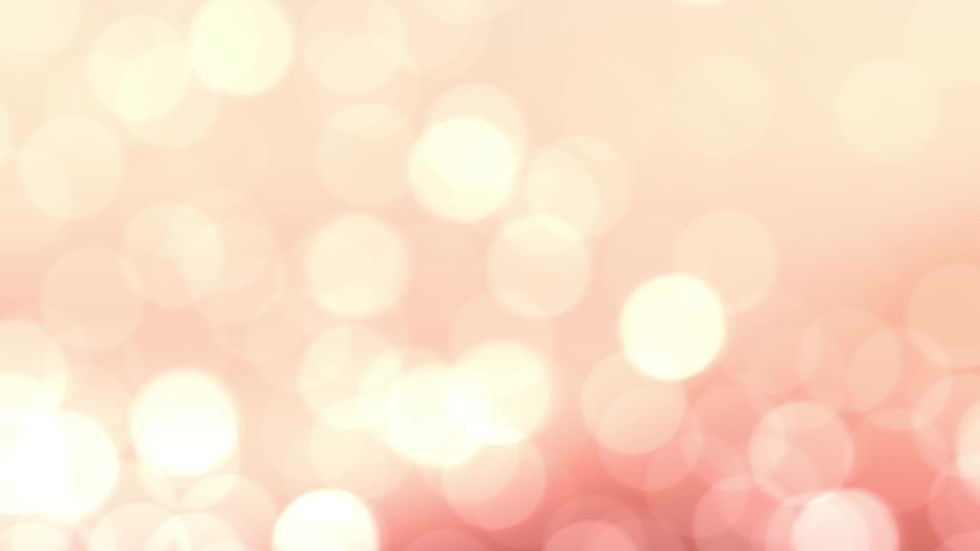
WHO WE ARE
We have been conducting various research government and industrial projects, and supporting customer's R&D works. R&D director, has long R&D experiences for CFD, FEM, CSD, MBD, Aeroelasticity, and FSI/FIV fields. He was also original developer of general purpose easy-to-use fluid-structure interaction (FSI) analysis solvers: FSIPRO2D and FSIPRO3D.
Based on our various and deep R&D experiences, you can expect one-stop CAE and experimental solutions related to the areas of structural mechanics, vibrations, fluid mechanics, fluid-structure interaction, heat transfer, and fatigue problems, etc. We have been also serving various R&D and engineering consultings for major huge indusrties, venture companies, and research institutes of South Korea. Just tell us your engineering design and verification problems, and you can get the best engineering solutions from us using our unique advanced technology, experience, and various experimental facilities. Complex multiphysical and multidisciplinary problems in real engineeing fields have been given to us, and those problems have been successfully solved to developed new R&D product and to satisfiy our customers.
Try to contact us first with your most difficult engineering problems, and all the preliminary consulting works are mostly free even before making contranct between you and us. Up on your requestments, well-consructed CAE models with full technical documents can be optimally supplied to you. We are aming one-stop CAE and TEST service since we have multiphysical expert engineering teams, excellent expeirmental facilities, and strong engineernig networks covering the area of CFD, FEM, CSD, FMBD, FSI/FIV, and experimental test. Various experimental facilities we have constucted so far and continuously expanding till now. Extra services for real scale and scaled mock-up production can be supploed using our 3D RP (rapid-prototyping) machine such as FORTUS 900mc. Your requested mock-up models can be accurately generated based on the designed CAD model using ABS materials and combined construction technology with composite materials.
​
OUR R&D MOVIE
[1] NONLINEAR TRANSONIC AEROELASTIC ANALYSIS
This movie files show the FSIPRO3D application results for a full configuration supersoinic fighter. In this simulation, we have successfully considered both the local motions of several control surfaces and the multiple external stores. The flight Mach number is about 0.92 and contoures indicate the distributions of Mach numbers. You can also see the normal shock waves patterns on the aircraft surfaces in the transonic regime. The FSIPRO3D code is a general purpose 2-way coupling fluid-stucture interaction analysis code which was developed by Prof. Dong-Hyun Kim. He has been developed several aeroalstic analysis code based on the transonic small-disturbance (TSD), full potential equations (FPE), Euler and Navier-Stokres equations. He also wrote several journal papers related to the topics of computational aeroelasticity, FSI, and FIV problems.
[2] STORE-INDUCED FLUTTER ANALYSIS IN A TRANSONIC FLOW
Following movie (left) shows the non-conventional non-linear flutter phenominon due to the existance of a pylon/store in the transonic flow. If the wing has no store, there was no flutter phenomon for the same inflow Mach number of 0.97.
[2] WIND TUNNEL TEST of WIND TURBINES
In august 2014, a large wind tunnel facility was constructed in the main campus of Gyeongsang National University (GNU), Jinju city, South Korea. Prof. D.H. Kim designed this wind tunnel and was the director of this wind tunnel TEST-BED constuction project and then he has been managing the wind tunnel test center of GNU. This wind tunnel was specially designed for the performance and safety tests of small wind turbines. However, the tests for a scale down model of a MW class wind turbine and realc scale industrial equpiments can be effectively conducted as well because of its big test section area. The GNU WT wind tunnel (open type) has 8 m x 8m wind area and 30 m lengh. The maximum operational wind speed is more than 45 m/s. The test wind turbine model (rotor diameter, D= 6m) has about 6 kW capacity@12 m/s and grid-tied inverter. The main benefit of the GNU wind tunnel is the generation of nature-like wind conditions including proper level of turbulence intensities (noramlly 5%~15%). In addition, it can control the distribution of wind speed (vertically and horizontally) by controlling the 9 units (3 x 3 array) of propeller fans.
[3] FLOW INDUCED VIBRAION ANALYSIS USING 2-WAY COUPLED CFD AND CSD METHODOLOGY
Flow-induced vibration analysis of a cascade model using FSIPRO2D code. Compressible turbulent viscous flow model and equivalent vibration model of the turbomachinary blade model were used based on the 2-way coupling method. Below movie (right) show the numerical moving and deforming grid with boundary layers that is essentially required during the CFD based stall flutter analysis of turbomachinary blades.
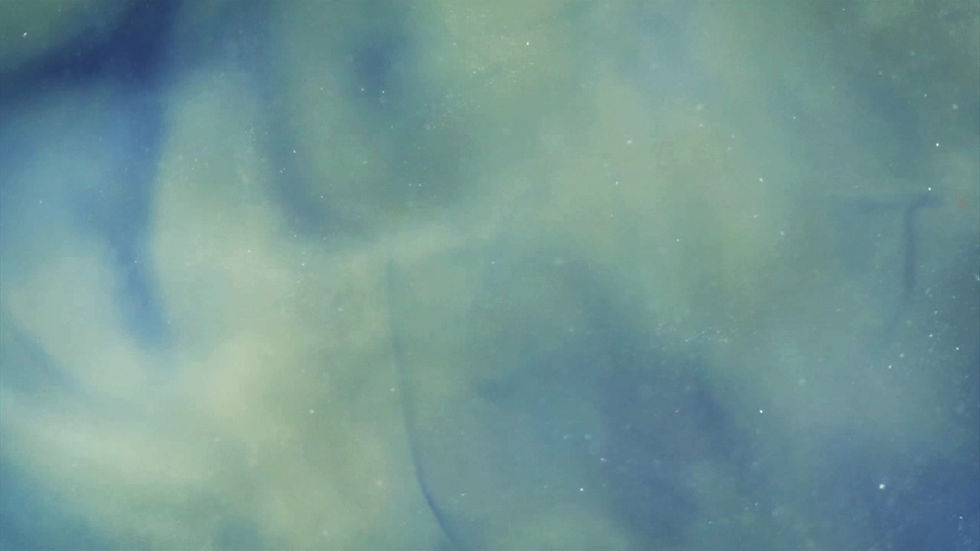